Focke Meler Gluing Solutions : deux innovations pour toujours mieux coller aux besoins des industriels
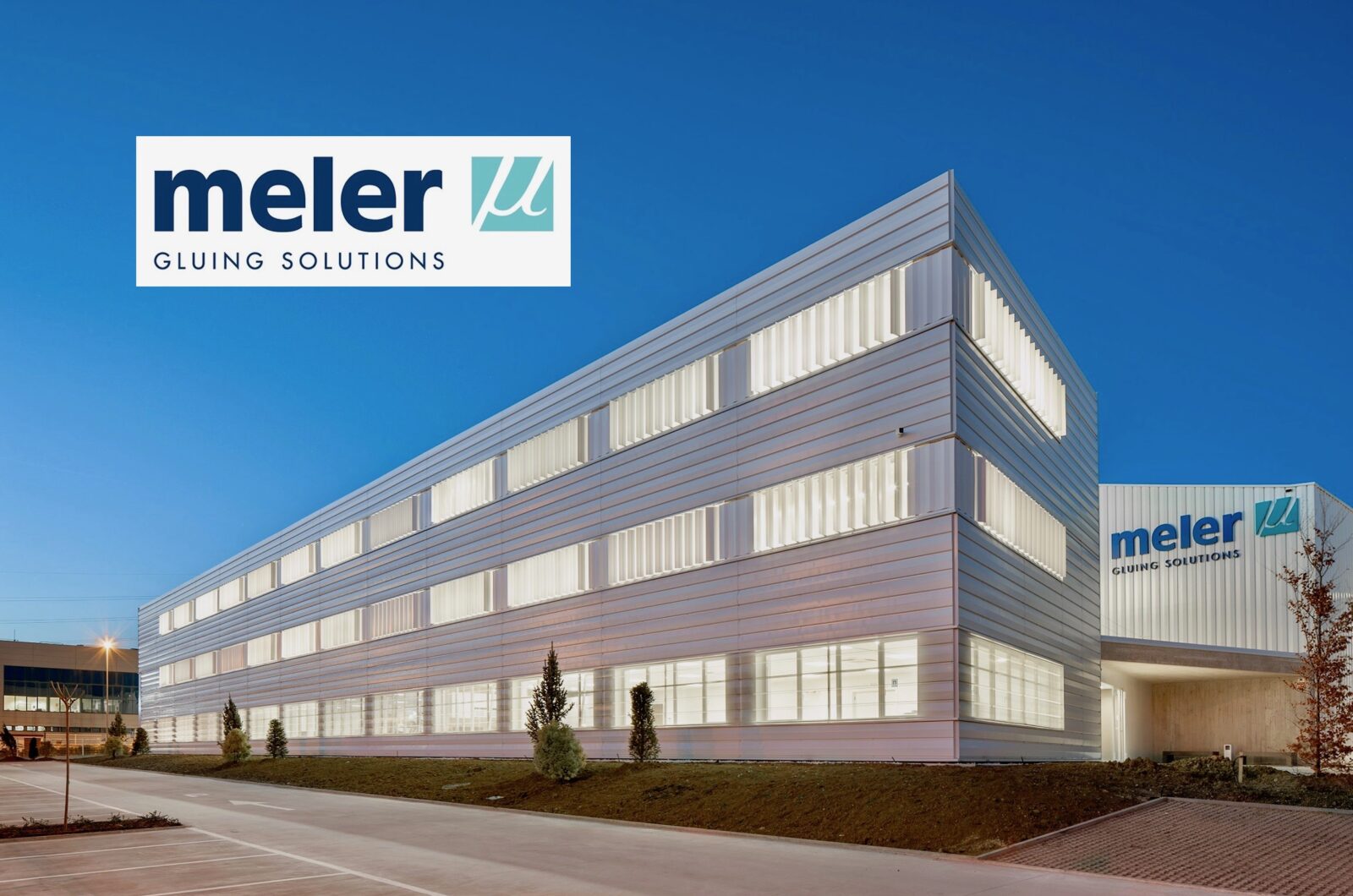
Le spécialiste des solutions d’application de colles industrielles pour de nombreux secteurs, au premier rang desquels l’ameublement (matelas, meubles, sièges, bois, transformation de mousse), a choisi de mettre en avant deux innovations : le “Raptor Handy” et le “Foaming”. Explications.
Vous connaissez Focke Meler Gluing Solutions ? Groupe espagnol d’envergure internationale (cinq filiales en Europe, une aux USA, présent dans plus de 30 pays), dont le siège se trouve sur la commune d’Arazuri, à coté de Pampelune, en Espagne, dans la province de Navarre, Focke Meler Gluing Solutions développe sa marque, Meler, depuis plus de trente ans maintenant, des solutions d’application de colles industrielles, pour répondre à une grande variété de besoins manufacturiers. Terme générique : “gluing solutions” (solutions de collage). Un savoir-faire largement éprouvé donc, grâce auquel l’entreprise propose aujourd’hui des réponses sur mesure à destination de l’industrie de l’ameublement. Sa filiale française (Focke Meler France), dirigée par Sylvain Pitard et implantée à Ingré (45), au nord-ouest immédiat d’Orléans, dispose d’une équipe commerciale et technique « totalement opérationnelle, pour accompagner les industriels de l’ameublement et du matelas, avec un accent tout particulier mis sur l’ergonomie des postes de travail et l’optimisation des processus ».
« Meler est spécialisée dans le développement de solutions complètes pour l’application d’adhésifs industriels dans de nombreux secteurs, dont celui de l’ameublement : matelas, meubles, sièges, bois, transformation de mousse… », résume Max Acdarian, directeur du développement commercial chez Impex New Co (entreprise d’import-export qu’il anime avec son épouse) et agent exclusif pour plusieurs fournisseurs majeurs de l’industrie, tels Elektroteks, Colcar, Nano Springs et, justement, Meler, « pour qui nous sommes les agents exclusifs sur la France et la Belgique dans l’industrie de la literie, du siège et la transformation de mousse », ajoute ce professionnel bien connu des acteurs de la filière, dont les compétences ne sont plus à prouver, notamment sur le secteur de la literie.
« L’adhésif thermofusible est sans conteste la solution de collage la plus employée dans la fabrication des matelas, explique-t-il. Elle apparaît en outre comme la plus aisée à intégrer dans les processus de production automatisés, ceci grâce à un séchage quasi immédiat. L’utilisation d’une colle ou d’une autre dépend du type de production. Or Meler dispose d’un tel savoir-faire, spécialisé dans les applications de colles thermofusibles, qu’il est en mesure de proposer des solutions complètes, adaptées à chaque fabricant ».
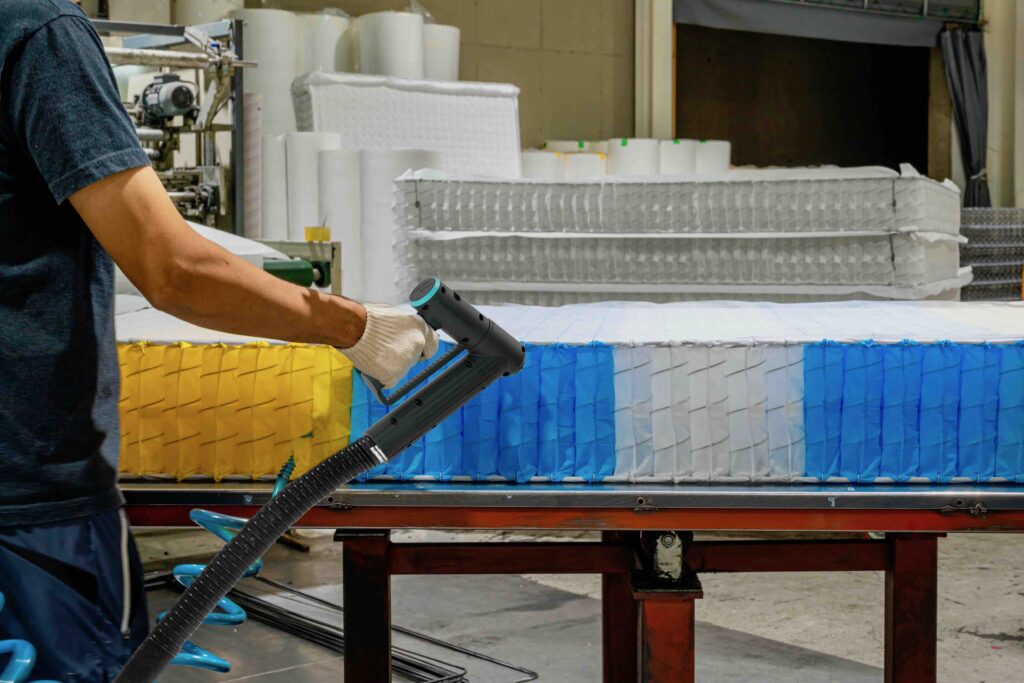
Fort de cette capacité d’optimisation des processus, le spécialiste a choisi de mettre en avant deux innovations : le “Raptor Handy” et le “Foaming”.
Le “Raptor Handy”, lauréat en 2022 des prestigieux “ADI Awards” et “Red Dot Design Award”, est un nouvel applicateur manuel. Ses principaux atouts : une nouvelle gâchette ergonomique et une capacité de rotation du tuyau à 360°. La flexibilité offerte par Meler permet à l’utilisateur de configurer l’applicateur en usine en fonction des besoins de production de sa ligne.
Meler dispose également d’une nouvelle technologie : le “Foaming” des adhésifs thermofusibles. Cette technique, basée sur l’obtention d’un mélange équilibré entre air et colle, offre de grands avantages de production. Elle permet notamment de réduire la consommation de colle, d’augmenter le volume du cordon/fibérisation de matière et d’étendre la surface d’adhérence sur le support à encoller. En outre, le “temps ouvert” est légèrement augmenté et permet le repositionnement des couches avec un ajustement « rapide et propre ». À l’intention des industriels qui seraient intéressés par cette technologie, Meler a d’ailleurs lancé le “Micron + FOAM”, premier fondoir compact (pour le moussage des adhésifs thermofusibles) qui, outre le fait qu’il offre un triple avantage aux industriels (15 % d’économies d’énergie, jusqu’à 20 % de réduction de la consommation d’adhésif et enfin une diminution de poids des produits finis), « permettra à de nombreuses entreprises de tester les gains de la technologie “Foaming”, à un niveau d’investissement raisonnable », conclut Max Acdarian.